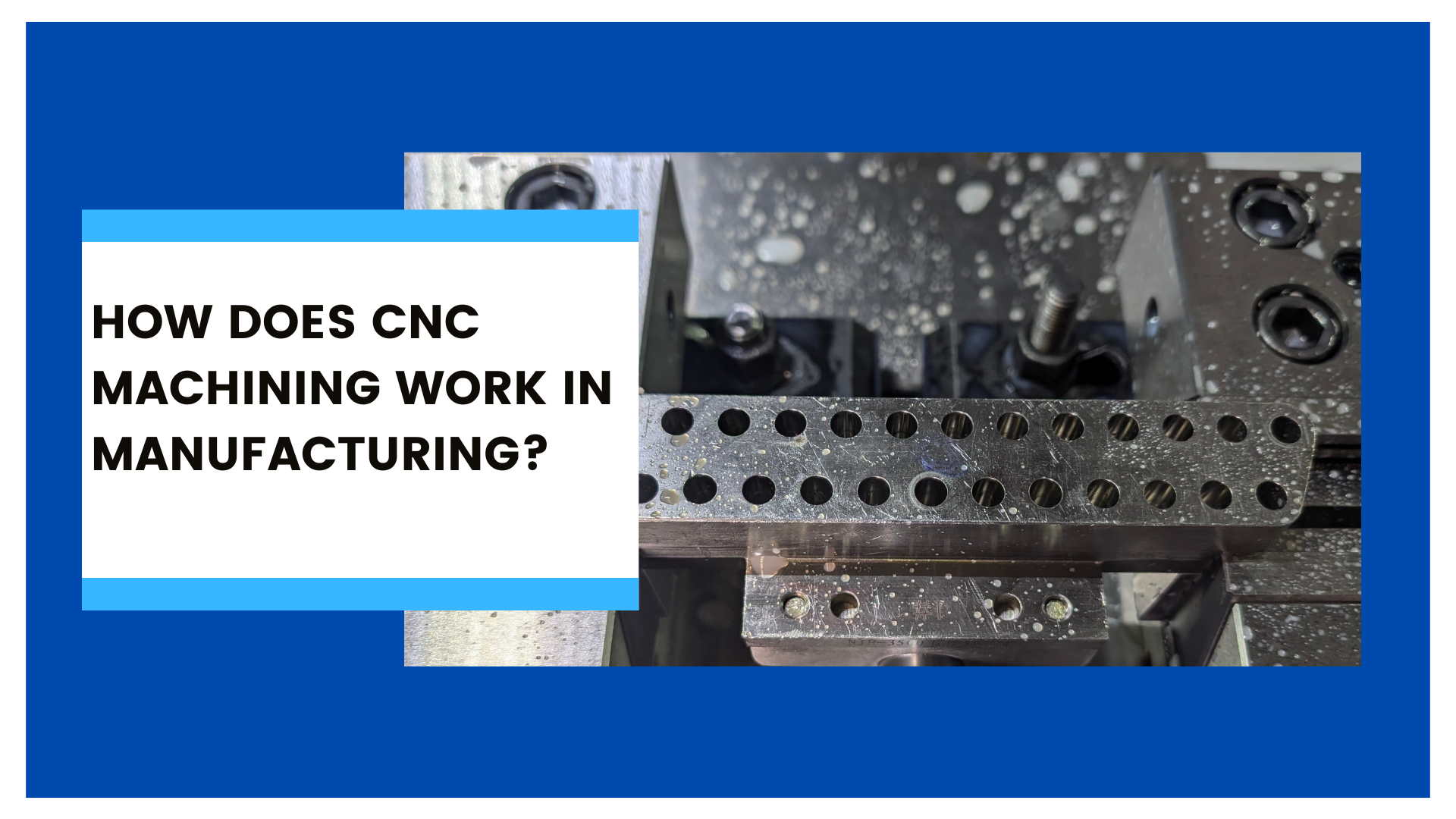
Table of Contents
CNC machining has transformed modern manufacturing by enabling unprecedented accuracy and efficiency in producing complex parts. With roots that trace back to innovations in the 1950s, this technology has evolved into a critical asset for industries ranging from aerospace and automotive to electronics and healthcare.
CNC milling machining services have become indispensable for achieving high-quality production outcomes. Here, we will explore the fundamentals of CNC machining, its core components, process workflow, and the various types of machines that drive the industry forward.
I. What is CNC Machining?
CNC, or Computer Numerical Control machining, is a subtractive manufacturing method where pre-programmed computer software directs the movement of factory tools and machinery. It involves removing material from a solid block - metal, plastic, wood, or stone to form a desired part or product. The process begins with a digital design converted into precise instructions, ensuring consistency and accuracy in every production run. By leveraging CNC manufacturing, manufacturers can achieve tight tolerances and intricate geometries that were once difficult or impossible to replicate using traditional machining methods. This technology has continuously adapted to meet the demands of modern production, making it the backbone of numerous industries seeking rapid prototyping and mass production.II. Key Components of a CNC Machine
A typical CNC machine is composed of several interrelated components that work together to transform digital designs into tangible parts:- Central Processing Unit (CPU): The brain of the operation, the CPU interprets the part program, usually a series of G-code and M-code instructions, and converts it into precise movement commands.
- Machine Control Panel: This interface allows operators to load, modify, and monitor the CNC program. It is essential for setting reference points and ensuring that all machine operations align with the intended design.
- Machine Tool: The machine tool, including the spindle and cutting tools, physically shapes the workpiece. CNC machining milling is responsible for the detailed cuts and shaping needed for high-precision components.
- Programmable Logic Controller (PLC): PLCs manage logic-based decisions and automate auxiliary functions, reducing manual intervention and enhancing overall production efficiency.
- Servo Control Unit and Feedback Devices: Sensors monitor the position and speed of the cutting tool, adjusting the commands in real-time for precision, ensuring every moment is accurate.
- Display Unit: A critical interface for diagnostics and real-time monitoring, the display unit provides vital data such as error messages, program status, and machine parameters.
III. The CNC Process Workflow
The CNC process unfolds through a series of well-defined steps, ensuring that each part meets exact specifications:- Design and CAD/CAM Preparation: The journey starts with a detailed computer-aided design (CAD) model that outlines every dimension and feature of the part. Designers use computer-aided manufacturing (CAM) software to translate these models into machine-readable instructions. The same software family can handle many cases using CAD and CAM functions, streamlining the transition from design to production.
- CNC Programming: CAM software generates a CNC program composed of coordinate-based instructions using standardised G-code and M-code languages. This program dictates everything from the cutting path to tool changes, forming the blueprint for the machining process.
- Material Setup and Parameter Selection: Choosing the right material is crucial. CNC machining services handle various substrates—from robust metals to composite materials—and set the appropriate cutting speeds, tool types, and machining parameters to achieve optimal results.
- Execution and Quality Control: Once programmed and set up, the CNC machine reads the instructions and begins cutting and shaping the workpiece. The machine’s precision allows for minimal error, high repeatability, and a significantly reduced production cycle compared to manual methods.
IV. Common Types of CNC Machines
Different types of CNC machines are required for specific manufacturing needs, each with its own set of advantages:- CNC Milling Machines: This machine, known for its accuracy, can perform intricate cutting and shaping tasks. In CNC milling machining, multi-axis systems, ranging from 3-axis to advanced 5-axis setups, facilitate the production of highly complex components with superb precision.
- CNC Lathes: Ideal for producing cylindrical parts, CNC lathes rotate the workpiece against a cutting tool, ensuring uniformity in parts that require symmetry. It is particularly valuable in industries like automotive manufacturing.
- CNC Plasma and Laser Cutters: These machines can cut through robust materials. Plasma cutters utilise high-temperature plasma torches, while laser cutters harness concentrated laser beams for precise cuts. Both are used extensively in metal fabrication and intricate design work.
- CNC Electric Discharge Machines (EDM): For highly detailed and complex work, electric discharge machines use electrical discharges to erode material away, making them indispensable for the mould and die industry.
V. Advantages of CNC Machining
The benefits of CNC machining are many, making it a popular choice for modern production environments:- Efficiency and Repeatability: Once programmed, CNC machining milling and other services can produce high volumes of parts with superior consistency.
- Versatility: Whether dealing with metals, plastics, or composite materials, CNC manufacturing processes are adaptable to various substrates.
- Speed and Accuracy: Automated operations significantly reduce production times while ensuring that each component meets exact design specifications.
- Reduced Waste: Optimised nesting and precise cuts lower material waste, making CNC processes cost-effective and environmentally friendly.