
Table of Contents
With manufacturing evolving so quickly, precision and efficiency have become paramount. Computer Numerical Control (CNC) machining, a technology revolutionising production processes across various industries.
CNC machining enables manufacturers to produce complex components with remarkable accuracy and consistency. By automating the control of machining tools through computer programming, CNC systems minimise human error and enhance productivity. This advancement has been instrumental in meeting the high demands of sectors such as aerospace, automotive, and healthcare.

CNC Machining as the Backbone of Modern Manufacturing
In today's advanced manufacturing landscape, Computer Numerical Control (CNC) machining stands as a cornerstone technology. Its precision and efficiency have become indispensable across various sectors, notably in aerospace, defence, and general engineering. From crafting intricate components for aircraft to producing robust parts for military applications, CNC machining ensures that industries meet the highest standards of quality and performance. Companies like MK CNC Engineering, based in Queensland, exemplify Australia's leadership in this domain. Specialising in high-precision CNC machining, they serve critical sectors including aerospace, mining, defence, and general engineering, delivering components that meet stringent industry requirements.Purpose of the Guide: What You'll Learn
This comprehensive guide aims to demystify CNC machining by exploring:- The various CNC machining processes and their functionalities.
- The tangible benefits these technologies bring to modern manufacturing.
I. What is CNC Machining?
CNC machining is an advanced manufacturing process that utilises computerised controls to operate and manipulate machine tools. Unlike traditional manual machining, CNC machining automates the control of tools like lathes, mills, routers, and grinders through pre-programmed software, ensuring high precision and consistency in producing complex parts. The evolution from manual to CNC machining marked a significant shift in manufacturing. Early numerical control systems in the 1940s and 1950s relied on punched tape to guide machines. With the advent of digital computers in the 1960s, these systems transformed into CNC machines, offering enhanced flexibility, accuracy, and efficiency in production processes.How CNC Machining Works
The CNC machining process begins with a digital design created using Computer-Aided Design (CAD) software. This design is then converted into a set of instructions by Computer-Aided Manufacturing (CAM) software, which translates the design into G-code, a language that CNC machines understand. The CNC machine executes these instructions, precisely cutting and shaping the material into the desired form. Common CNC machines include:- CNC Milling Machines: Used for cutting and drilling materials with rotating multi-point cutting tools
- CNC Lathes: Rotate the workpiece against a cutting tool to shape it.
- CNC Drilling Machines: Specialised to create precise holes in materials.
History and Evolution
The journey of CNC technology began in the late 1940s with the development of numerical control (NC) machines. By the 1950s, the integration of computers led to the emergence of CNC machines, revolutionising manufacturing processes. Key milestones in CNC evolution include:- 1960s: Introduction of digital control systems, enhancing machine flexibility.
- 1970s: The Development of microprocessors made CNC machines more accessible and efficient.
- 1980s: Advancements in software and hardware led to widespread adoption in various industries.
- 2000s-Present: Integration of CAD/CAM software, real-time monitoring, and automation, further improving precision and productivity.
II. Core CNC Machining Processes
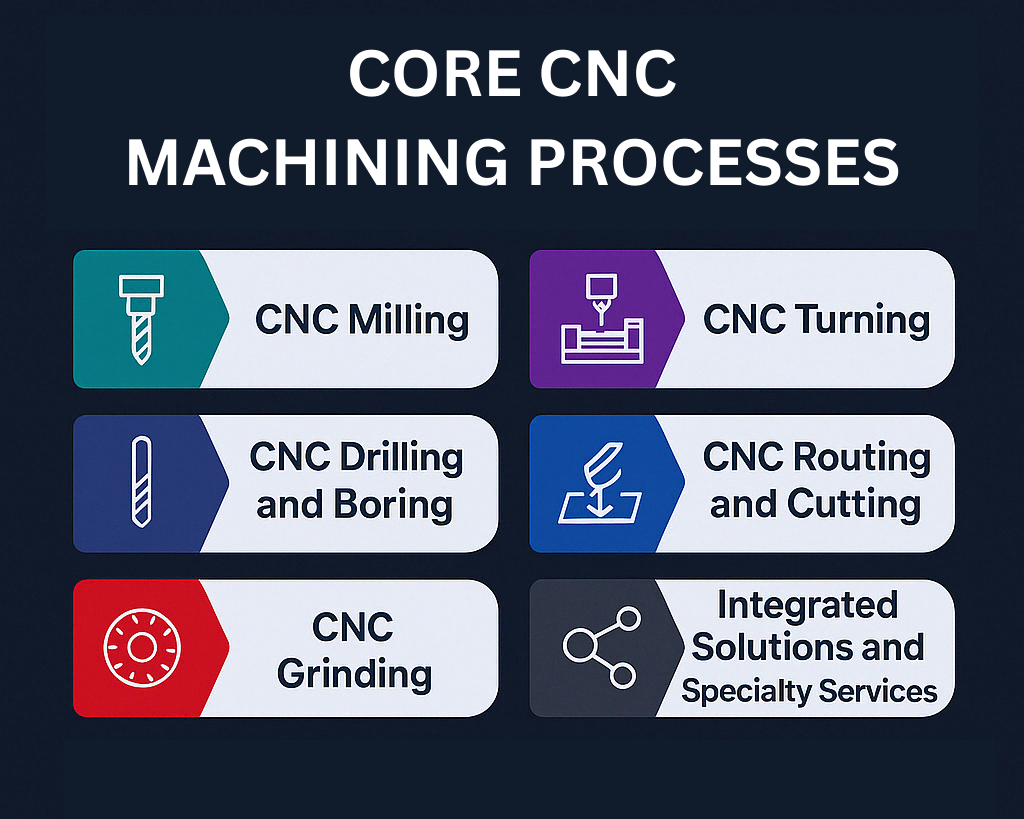
1. CNC Milling
CNC milling employs rotary cutters to remove material from a stationary workpiece. Guided by computerised controls, the milling machine executes precise movements to shape the material into the desired form. Widely used in industries like automotive and aerospace, CNC milling is ideal for creating complex parts, moulds, and components with intricate geometries.Advantages:
- High precision and repeatability
- Versatility across various materials
- Suitable for both small and large production runs.
2. CNC Turning
CNC turning involves rotating the workpiece while a stationary cutting tool shapes it. This process is typically performed on a lathe and is optimal for producing cylindrical parts. Essential for manufacturing shafts, rods, and other round components requiring tight tolerances.Advantages:
- Efficient for high-volume production
- Maintains consistent quality
- Cost-effective for producing symmetrical parts
3. CNC Drilling and Boring
CNC drilling uses rotating drill bits to create precise holes in a workpiece. Boring, on the other hand, enlarges existing holes to achieve greater accuracy and finish. Crucial in sectors like aerospace and automotive, where exact hole placement and dimensions are vital for assembly and performance.4. CNC Routing and Cutting
This category includes methods like laser cutting, waterjet cutting, and plasma cutting. These processes use different energy sources to cut materials with high precision. Ideal for producing detailed cuts in various materials, these methods are used in both prototype development and final product manufacturing.Advantages:
- Ability to cut complex shapes with precision
- Minimal material wastage
- Suitable for a wide range of materials
5. CNC Grinding (and Other Finishing Processes)
CNC grinding involves using a rotating abrasive wheel to remove material, achieving high surface quality and dimensional accuracy. Commonly used in industries like defence and aerospace, where components require fine finishes and exact tolerances.Advantages:
- Exceptional surface finish quality
- High precision for tight tolerances
- Suitable for hard materials
6. Integrated Solutions and Specialty Services
Beyond standard machining, advanced CNC capabilities include wire EDM (Electrical Discharge Machining) and custom fixture manufacturing. Wire EDM uses electrical discharges to cut intricate shapes in hard materials, while custom fixtures are designed to hold parts during machining, enhancing precision and efficiency. These services are essential for producing complex components and ensuring consistent quality in mass production.Advantages:
- Ability to machine intricate and delicate components
- Improved accuracy and repeatability
- Enhanced production efficiency
IV. Types of CNC Machines

1. CNC Milling Machines
Functionality: CNC milling machines utilise rotary cutters to remove material from a workpiece, shaping it into the desired form. They are widely used in industries such as aerospace, automotive, and medical device manufacturing to create complex parts and components.3-Axis vs. 5-Axis Milling:
- 3-Axis Milling: Involves movement along the X, Y, and Z axes. Suitable for simpler parts and operations like drilling and slotting.
- 5-Axis Milling: Adds two rotational axes, allowing the tool to approach the workpiece from multiple angles. Ideal for intricate and complex geometries, reducing the need for multiple setups and improving accuracy.
2. CNC Lathes
Turning Operations and Suitable Parts: CNC lathes rotate the workpiece against cutting tools to perform operations like turning, facing, and threading. They are essential for producing cylindrical parts such as shafts, rods, and bushings.Advantages Over Traditional Lathes:
- Precision: CNC lathes offer high accuracy and repeatability.
- Efficiency: Automated operations reduce production time.
- Flexibility: Capable of handling complex designs and multiple operations in a single setup.
3. Other CNC Machines
Plasma Cutters, Laser Cutters, and EDM Machines:
- Plasma Cutters: Use electrically conductive gas to cut through metals. They are commonly used in automotive repair and industrial fabrication.
- Laser Cutters: Employ a focused laser beam for high-precision cutting. They are widely used in electronics, medical devices, and signage industries.
- EDM (Electrical Discharge Machining): Removes material using electrical discharges. Ideal for intricate and hard-to-machine parts in aerospace and tool-making sectors.
V. Benefits of CNC Machining

Precision and Accuracy
CNC machines achieve exceptional precision, with tolerances as fine as 0.004 mm. This level of accuracy is crucial in sectors like aerospace and defence, where components must meet stringent specifications. Advanced software and rigorous quality control measures, such as Coordinate Measuring Machines (CMM) and laser interferometry, ensure consistent quality and minimise errors.Efficiency and Scalability
Automation in CNC machining significantly enhances production speed. Once programmed, CNC machines can operate continuously with minimal human intervention, making them ideal for both small-batch prototyping and high-volume manufacturing. This scalability allows manufacturers to meet varying production demands efficiently.Flexibility and Customisation
CNC machining offers remarkable flexibility, enabling quick modifications to digital designs before production. This adaptability allows manufacturers to respond swiftly to design changes or new requirements, reducing downtime and accelerating product development cycles.Repeatability and Reliability
CNC machines ensure that each component is manufactured to the exact same specifications, regardless of production volume. This repeatability is essential for industries with strict regulatory standards, such as medical device manufacturing, where consistency and reliability are paramount.Reduced Waste and Cost-Effectiveness
Optimised machining paths and precise material removal in CNC machining lead to minimal waste. This efficiency not only conserves materials but also results in significant cost savings over time, making CNC machining a cost-effective solution for manufacturers.Enhanced Safety and Automation
CNC machining reduces the need for manual intervention, thereby enhancing operator safety. Integrating CNC systems with Industry 4.0 initiatives enables real-time monitoring and predictive maintenance, further improving operational safety and efficiency.VI. Applications Across Diverse Industries
CNC machining is a cornerstone of modern manufacturing, delivering precision, efficiency, and adaptability across many industries. From aerospace to medical devices, its applications are vast and critical.Aerospace and Aviation
In aerospace manufacturing, CNC machining is crucial for producing components that must withstand extreme conditions and meet stringent safety standards. Critical parts such as turbine blades, compressor discs, airframe structures, and landing gear components are crafted with micron-level precision to ensure optimal performance and safety.Defence and Military
The defence industry relies heavily on CNC machining to manufacture robust and reliable components for military equipment. From firearm parts like receivers and barrels to complex systems in aircraft and naval vessels, CNC processes ensure that each component meets exacting specifications and can withstand harsh operational environments.Mining and Heavy Industry
CNC machining for mining applications plays a vital role in fabricating durable components used in excavation, drilling, and processing equipment. High-strength, wear-resistant parts are essential for withstanding the harsh conditions of mining operations.Mining and Heavy Industry
CNC machining for mining plays a vital role in fabricating durable components used in excavation, drilling, and processing equipment. High-strength, wear-resistant parts are essential for withstanding the harsh conditions of mining operations.Automotive and Transportation
CNC machining plays a pivotal role in the automotive industry by producing high-precision components essential for vehicle performance and safety. Engine parts such as cylinder heads, pistons, and crankshafts, as well as transmission components like gears and shafts, are manufactured with tight tolerances to ensure efficiency and reliability.General Engineering and Industrial Manufacturing
In general engineering and industrial manufacturing, CNC machining offers versatility in producing various components. From heavy machinery parts to custom fixtures, CNC processes enable the creation of complex geometries with high precision, catering to bespoke equipment needs across various sectors.Medical Devices and Equipment
The medical industry demands components with exceptional precision and reliability. CNC machining meets these requirements by producing intricate parts for surgical instruments, implants, and diagnostic devices. Materials like stainless steel, titanium, and medical-grade plastics are commonly used to ensure biocompatibility and durability.Offshore and Global Manufacturing
CNC machining facilitates offshore manufacturing by enabling companies to produce high-quality components that meet international standards and regulations. Many companies offer tailored solutions that combine cost-effectiveness with strict quality control, supporting global supply chains and diverse project requirements. CNC machining's adaptability and precision make it an invaluable asset across these industries. It drives innovation and ensures quality in every component produced.VII. Advancements and Emerging Trends in CNC Machining
The landscape of CNC machining is rapidly evolving, driven by technological innovations that enhance precision, efficiency, and adaptability. Below are some of the most significant advancements shaping the future of manufacturing:Integration with Digital Technologies
The fusion of CNC machining with digital technologies has ushered in a new era of smart manufacturing:- Internet of Things (IoT): Iot-enabled CNC machines provide real-time data on operational parameters, enabling predictive maintenance and reducing downtime. For instance, sensors can monitor temperature and vibration, alerting operators to potential issues before they lead to failures.
- Real-Time Monitoring: Advanced monitoring systems offer comprehensive visibility into machine performance, cycle times, and production rates, facilitating immediate corrective actions and continuous process improvement.
- Advanced CAD/CAM Software: Modern CAD/CAM software integrates seamlessly with CNC machines, allowing for precise toolpath generation and simulation. This integration streamlines the design-to-production workflow, reducing errors and enhancing product quality.
Automation and Industry 4.0
Industry 4.0 represents the next frontier in manufacturing, characterised by:- Enhanced Automation: Next-generation CNC machines feature increased automation capabilities, including robotic material handling and automated tool changers, which reduce human intervention and increase throughput.
- Smart Factories: Smart factories involve interconnected machines and systems that communicate and make autonomous decisions. This interconnectedness leads to optimised production schedules, reduced waste, and improved efficiency.
- Collaborative Robotics (Cobots): Cobots work alongside human operators, enhancing flexibility and safety in manufacturing environments. They can perform tasks such as assembly, inspection, and packaging and adapt to changes in production requirements.
Innovations in Materials and Methods
Recent developments in materials and machining methods have expanded the capabilities of CNC machining:- Composite Materials: Advancements in machining techniques enable the precise processing of composite materials, such as carbon fibre and aramid fibre, which are increasingly used in aerospace and automotive for their exceptional strength-to-weight ratios.
- Hybrid Manufacturing: Hybrid CNC machines combine additive (3D printing) and subtractive (CNC machining) processes, enabling the creation of complex geometries with enhanced material properties. This integration reduces material waste and shortens production cycles.
- Sustainable Practices: Manufacturers are adopting sustainable practices, such as optimising machining paths to minimise energy consumption and utilising recyclable materials, which contribute to environmentally responsible production.
VIII. Choosing the Right CNC Machining Partner
Selecting the ideal CNC machining partner is crucial to ensuring the success of your manufacturing projects. The right partner brings not only technical expertise but also a commitment to quality, reliability, and customer satisfaction.Key Considerations
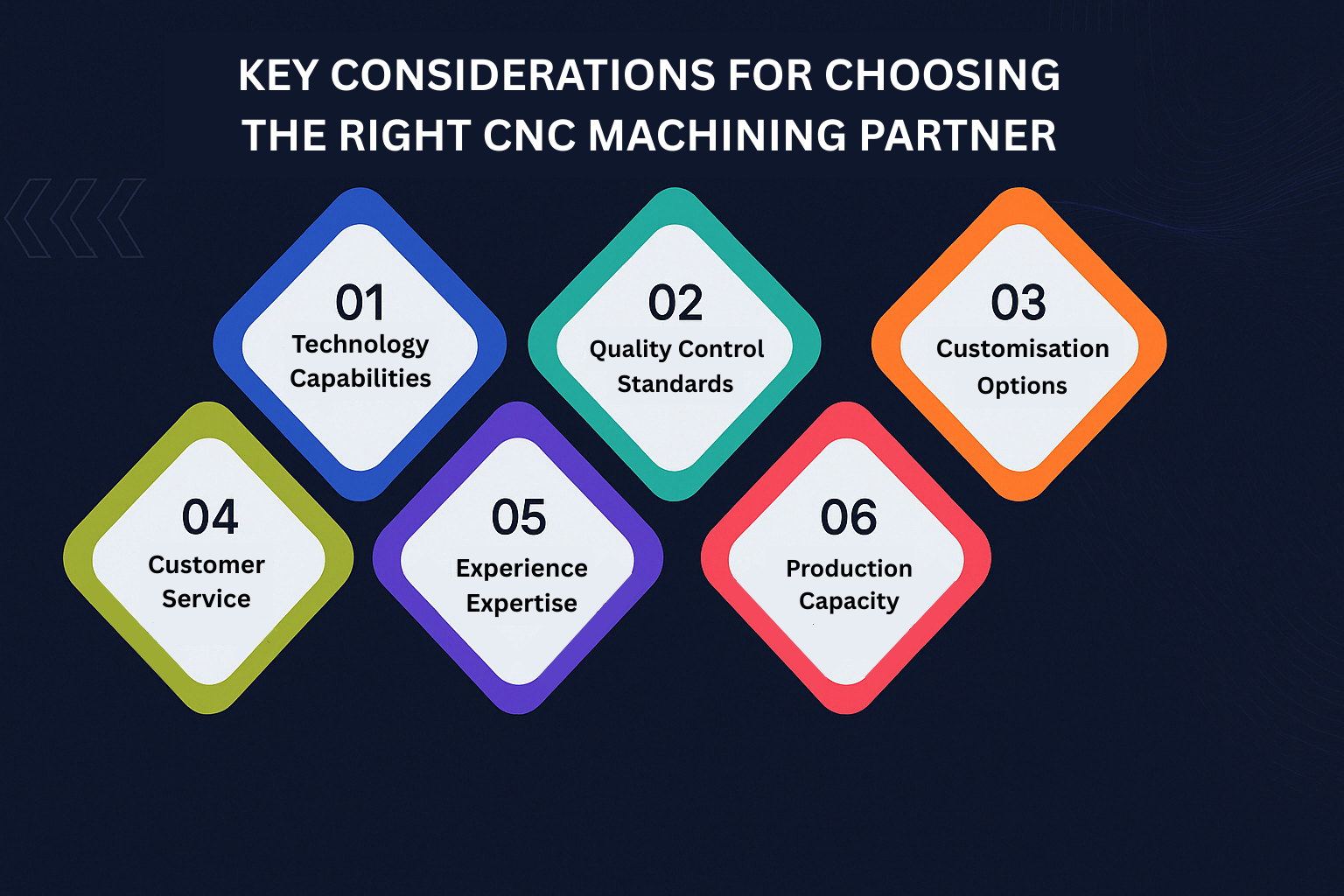
- Technology Capabilities: Ensure the provider utilises advanced CNC machinery and software to handle complex geometries and maintain tight tolerances.
- Quality Control Standards: Consider certifications such as ISO 9001, indicating adherence to stringent quality management systems. Inquire about their inspection processes and equipment used to guarantee consistent product quality.
- Customisation Options: A flexible partner should offer tailored solutions, accommodating specific design requirements and material preferences.
- Customer Service Excellence: Effective communication and responsive support are vital. Assess their willingness to collaborate, provide updates, and address concerns promptly.
- Experience and Expertise: A proven track record in your industry indicates familiarity with sector-specific standards and challenges.
- Production Capacity and Lead Times: Ensure they can meet your volume requirements within acceptable timeframes and offer scalability for future needs.
Why Choose MK CNC Engineering:
MK CNC Engineering offers a comprehensive suite of services, including specialised tool and fixture manufacturing. Their expertise ensures tailored solutions that address diverse production challenges, delivering superior quality and precision across various projects. MK CNC Engineering is a premier provider of precision engineering and manufacturing solutions in Australia. Here's why partnering with them is advantageous:- State-of-the-Art Machinery: Utilising advanced CNC technology, MK CNC Engineering delivers high-quality, precise components across various industries.
- Extensive Industry Experience: With a strong foundation built on years of industry experience, they specialise in delivering high-quality CNC engineering work to meet diverse client needs.
- Customised Solutions: Their team of experts transforms complex challenges into opportunities, blending technical mastery with creative insight to provide tailored solutions.
- Commitment to Quality: Dedicated to quality and reliability, MK CNC Engineering ensures every project is a milestone in engineering excellence.
- Customer-Centric Approach: They work closely with clients, turning challenges into opportunities for innovation and growth, ensuring exceptional value in every project.
How to Get Started
Engaging with MK CNC Engineering is straightforward:- Initial Consultation: Reach out to discuss your project requirements and objectives.
- Request for Quote: Provide detailed specifications to receive a comprehensive quote tailored to your needs.
- Project Planning: Collaborate with their engineering team to finalise designs, select materials, and establish timelines.
- Production and Delivery: Once approved, production commences, with regular updates provided until the delivery is complete.