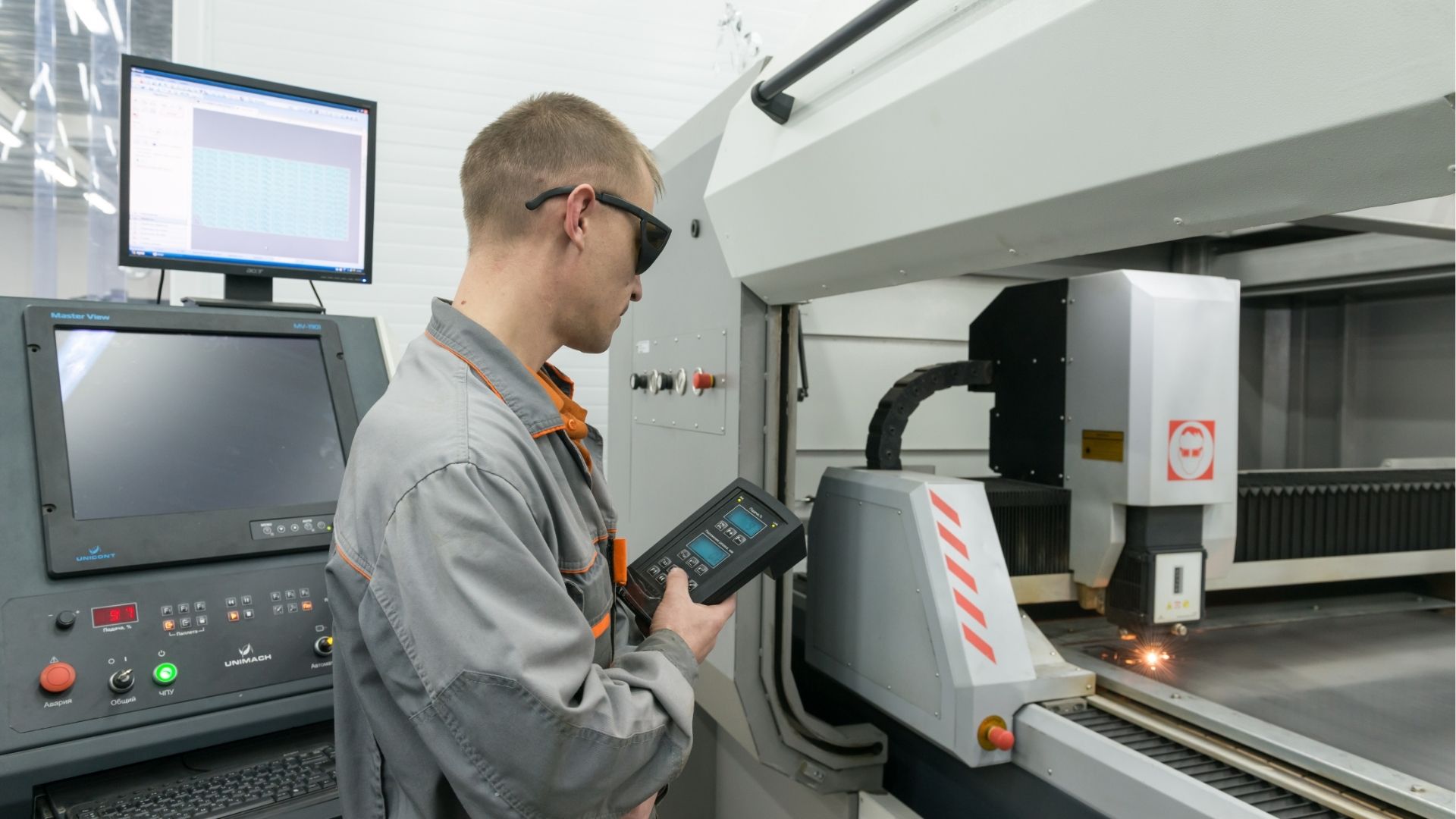
I. Core Advantages of CNC Machining
➤ Robust Performance: CNC machining achieves the stringent dimensional, tolerance, and performance standards necessary to prevent component failure. This process accommodates the production of aerospace parts using difficult-to-machine materials such as titanium, ensuring safe operation in demanding conditions.
➤ Accuracy: As technology continues to improve, CNC machining delivers consistently precise results. The enhanced accuracy, coupled with robust process controls, minimises the occurrence of defects, ensuring that aerospace parts perform reliably throughout their service life.
➤ Optimised Weight: For flying equipment, every gram counts. The process can produce thin-walled components and structures using lightweight yet strong materials, which is essential for achieving a favourable strength-to-weight ratio in aerospace applications.
➤ Increased Efficiency: A single CNC machine can execute multiple machining processes. The automation involved in CNC machining considerably speeds up production cycles while maintaining high output quality, which is beneficial in meeting tight production schedules.
➤ Cost-Effective Production: With rapid production cycles and precise material utilisation, CNC machining reduces waste and labour costs. This efficiency minimises the need for rework and lowers overall manufacturing expenses, making the process a financially viable option for aerospace manufacturing.
II. Applications Across the Aerospace Sector
➤ Seating Components: Aircraft and spacecraft seating demand careful consideration of weight and strength. Aluminium and other CNC-machinable metals are frequently processed to produce robust yet lightweight seating structures contributing to overall efficiency.
➤ Oxygen Generation Systems: Reliable aerospace components include parts for oxygen generation and safety systems. CNC machining allows for the formation of lightweight yet durable parts, delivering performance even under extreme operational conditions.
➤ Power Transfer Shafts: Critical for delivering power in aerospace applications, shafts must operate reliably under intense conditions. CNC machining makes these parts from heat-resistant materials, ensuring safe power transmission.
➤ Electrical Connectors: With stringent spatial and weight limitations, creating aerospace electrical connectors demands a process that ensures both precision and efficiency. CNC machining routinely produces connectors that maintain their performance despite the challenges posed by the aerospace setting.
➤ Structural Housings: The large and often intricate housings found in missiles and other aerospace vehicles call for a process that can handle both size and complexity. CNC machining delivers robust and meticulously crafted housings, providing a reliable solution for critical assemblies.
➤ Valve Assemblies: Small but critical valve components require high levels of precision to function effectively in the aerospace environment. CNC machining produces valves that operate safely and accurately, meeting the rigid specifications demanded by the industry.
➤ Filter Bodies: Complex geometries such as those seen in air and liquid filter bodies benefit significantly from the capabilities of CNC machining. These components can be machined in a single set-up, reducing turnaround times significantly while ensuring that all dimensions meet strict tolerance levels.
III. Material Selection for Machined Aerospace Parts
➤ Aluminium Alloy (Series 2xxx): This series, alloyed with copper, offers high strength while maintaining excellent machinability. It is commonly used in constructing wing and fuselage structures, contributing significantly to the aircraft's overall performance.
➤ Aluminium Alloy (Series 6xxx): This versatile series, composed of magnesium and silicon, resists corrosion and exhibits excellent formability and strength. Its properties make it a preferred material for several aerospace applications where durability is paramount.
➤ Aluminium Alloy (Series 7xxx): These alloys, which include zinc, copper, magnesium, and chromium, are highly strong and suitable for demanding military and high-performance aerospace applications.
➤ Exotic Metals: In addition to the standard alloys, MK CNC Engineering sources a wide range of materials, including stainless steel, high-stress alloys, carbon, and titanium. The selection is determined by each aerospace project's specific performance requirements and cost considerations, ensuring that every part is manufactured with the best-suited material.
Our expertise in aerospace machining enables the efficient fabrication of parts that adhere to stringent safety and performance standards and meet specific industry design requirements. Our understanding of the aerospace sector and advanced manufacturing techniques positions us as a preferred partner for those seeking dependable aerospace components.